Printed homes: housing of the future?
After gaining ground in a great many sectors, 3D printing is on its way to conquering the world of construction. The state-of-the-art of this revolutionary technique.
An investigation by Pierre-Yves Bocquet - Published on , updated on
The very first 3D-printed houses sprang up from the ground barely five years ago, and yet already such projects are multiplying around the world, from China and Russia to the United States and from the United Arab Emirates to the Netherlands and France. The fact is this new construction technique, based on additive manufacturing (which involves adding materials such as concrete layer by layer), affords many advantages: it allows buildings to go up in record time and at a lower cost, while offering architects great design freedom. After having conquered numerous other sectors, 3D printing is on its way to meeting the primary construction challenges: regularity and resistance. So much so that the technique, though still in its infancy, is being seen as the future benchmark method for fabricating buildings, and even as one of the most promising solutions to the housing crisis threatening a planet with a rapidly growing population.
One of the first on-site 3D-printed buildings
The offices of the Dubai Future Foundation, inaugurated in May 2016 in the United Arab Emirates, are among the world’s first fully functional 3D printed buildings. The printing was done on site by a six-metre-high robotic arm in just 17 days, and at a cost 50% lower than a traditional building of the same size (250 m2), according to the Dubai government. This Middle Eastern city, known for its dynamic real estate development – of which the world’s tallest tower, the Burj Khalifa, is emblematic – aims to have 2% of its new buildings fabricated using 3D printing by 2019, and 25% by 2025.
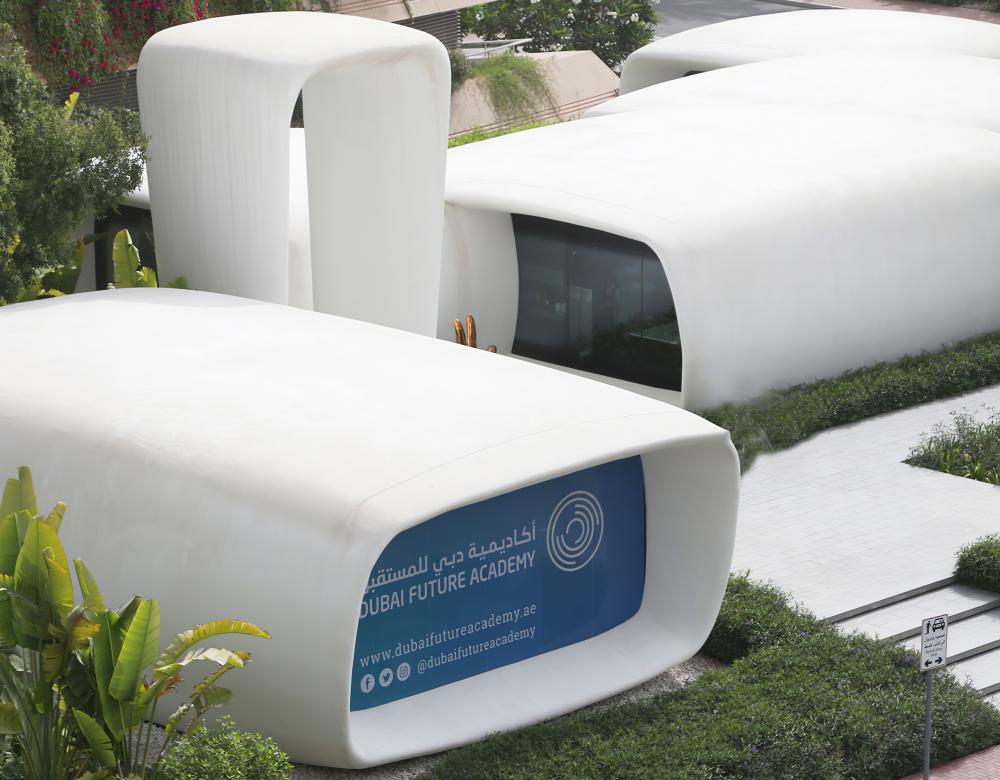
The difficult conquest of building
The building sector is the latest in a long list of industries attracted by the performances of 3D printing.
The 3D printing technique, which emerged in the late 1980s, involves laying down successive layers of material, joined together to make three-dimensional objects. Professionals also call the process ‘additive manufacturing,’ in contrast to conventional processes which involve removing material (cutting, planing, machining, sanding, etc.). Initially used for producing prototypes, 3D printing soon demonstrated the extent of its potential, as it has improved – particularly in speed and solidity – and as it has conquered numerous industries (aeronautics, automotive, medicine, etc.) thanks to a growing spectrum of materials, including polymer resin, plastic, metals, glass, ceramics, living cells, and, more recently, concrete. But before the building sector could benefit from its flexibility, its speed and its sobriety in raw materials – which rhyme with lower manufacturing costs – laboratories had to work quite some time to adapt the technique to the construction industry. First a new family of 3D printers capable of printing at construction scale had to be invented, and methods to deposit concrete layer by layer had to be devised. As a result, the first 3D-printed buildings did not appear until 2015.
No limit in size
Today’s increasingly large and powerful printers are making it possible to build big houses. Like this 640 m2 building under construction in Dubai, which is the largest 3D printed to date. The previous record was held by a two-storey, 400 m2 mansion in China. Experts say there is nothing in theory that stands in the way of fabricating 3D-printed buildings or towers one day.
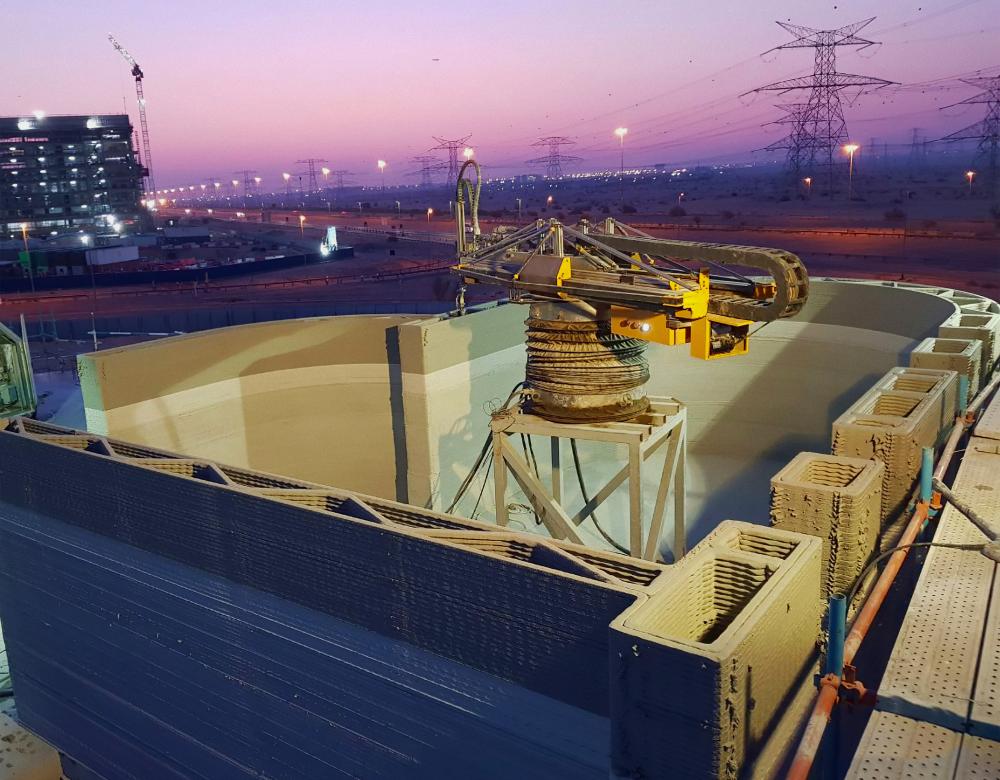
High technology concrete
Behind its apparent simplicity, the use of concrete in additive manufacturing presents a real challenge.
3D concrete printing uses the technique of extrusion, which consists in pushing a material through an orifice of a given cross-section (a nozzle) to give it the desired shape. Pushed through a pipe by a feeder screw or a pump, the concrete comes out of a nozzle that gives it a more or less flattened cylinder or ribbon shape. This technique is directly inspired by consumer 3D printers that deposit a filament of melted plastic, but it required surmounting several challenges specific to depositing concrete layer after layer. The concrete must have the right shape and consistency so that the deposited layer does not collapse under its own weight, and it must be robust enough to maintain its shape under the increasing weight of subsequent layers. The study of these constraints (an area of research called rheology) has led to the development of many different nozzle shapes, and the use of aggregates less than 4 millimetres in diameter in the composition of the concrete to achieve the desired consistency. Manufacturers also use additives, such as chloride or non-alkaline admixtures, to accelerate the setting, which is the moment the cement begins to dry, as well as the hardening, and consequently the long-term load resistance. These highly technical concretes, called “ultra-high performance” concretes, are up to five times more expensive than conventional concretes. But the advantages of 3D printing are such that this extra cost is quickly offset.
Concrete walls, but not only…
Ultimately, researchers hope to develop printers capable of depositing not only the concrete but also the insulation, electricity, etc. Initiated with concrete, 3D printed building is already beginning to diversify the materials used to integrate local resources, such as wood, straw or earth. Makeshift homes could be built in a few hours and at little cost to house, for instance, victims of natural disasters (cyclones, storms, earthquakes, etc.). 3D printing could also be extended to other building elements, starting with insulation. This was the case for a low-income housing project built in 2018 in Nantes: a concrete wall was poured between two layers of 3D-printed expansive foam. Having first served as formwork, the foam was then used for the final insulation of the building. But 3D printing is not limited to walls and partitions. A Swedish company, for example, developed a machine that can print doors and windows up to 1.5 metres wide and 2.5 metres tall using granulates in polymer or resin. Ultimately, builders are hoping to be able to print on the fly all the elements of a house: electrical wiring, furniture, fittings, roofing, etc. But this will require at least another ten years of research.
A liberation for design
Unlike conventional techniques, with 3D printing, making customized or original designs has little or no impact on the final cost of construction: only the quantity of material matters in this respect. For this reason, architects are overwhelmingly in favour of this technique, seeing it as a simple, flexible way to give free reign to their creativity.
Printing a base on another planet
Because of the benefits of using local materials, 3D printing is an appealing solution for building space bases.
Space agencies, particularly the European ESA and the American NASA, have been exploring for some years the best way to build a base on the Moon or Mars to house astronauts for long-duration missions. They are taking a close look for this purpose at 3D printing, as the technique enables the building of space habitats using raw materials collected locally, and consequently eliminates the need to transport heavy cargoes of material from Earth. Feasibility studies have shown that it would be possible, for example, to use regolith – the dust that abounds on the surface of our satellite – and harden it layer by layer using small robotic vehicles to inject a special binding solution which converts the material into a stone-like solid. This 3D printing technique has been tested on Earth, in vacuum, with a volcanic material similar to lunar soil. The sample wall blocks that were fabricated would make a perfectly acceptable base according to the ESA: their calculations indicate that printed walls 1 to 2 metres thick would shield against the harmful cosmic radiation emitted by stars and even against micrometeoroids.
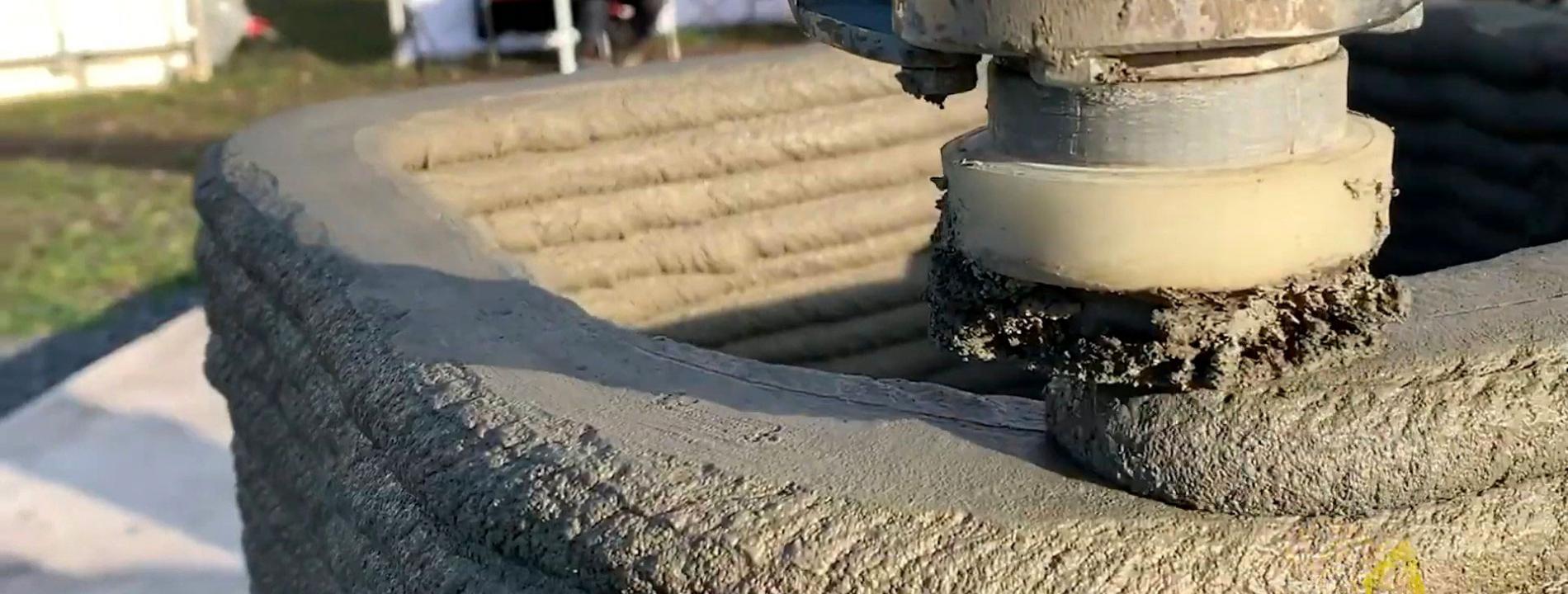
A response to the housing crisis?
As the global population continues to grow, 3D printing could contribute to resolving the housing crisis that threatens the planet.
According to its promoters, 3D printing is among the most promising solutions to the housing crisis threatening the future of our planet. Two major trends are important in this regard. First, the global population growth, from 7.7 billion today, to an estimated 9.7 billion by 2050 and 11 billion by 2100, according to the United Nations. That amounts to a 42% increase over a period of 80 years. Second, this population growth is accompanied by ongoing urbanization: according to the latest UN estimates, two out of three people may live in a city by 2050. That’s 2.5 billion more city dwellers than today! There is an urgent need as a result for new housing and even for the creation of new cities. One of the significant advantages of 3D printing over conventional construction techniques is the low cost of materials. Making the most of computer-aided design, the technique allows for reducing the amount of concrete used to a strict minimum: for example, instead of fabricating solid walls, hollow honeycomb structures inside the walls can provide tensile strength that is precisely tuned to the final requirements. The significant reduction in concrete use generates a virtuous circle by reducing the production and transport of materials, construction time, polluting emissions, waste on the construction site, and so on. All of which leads to substantial financial savings.
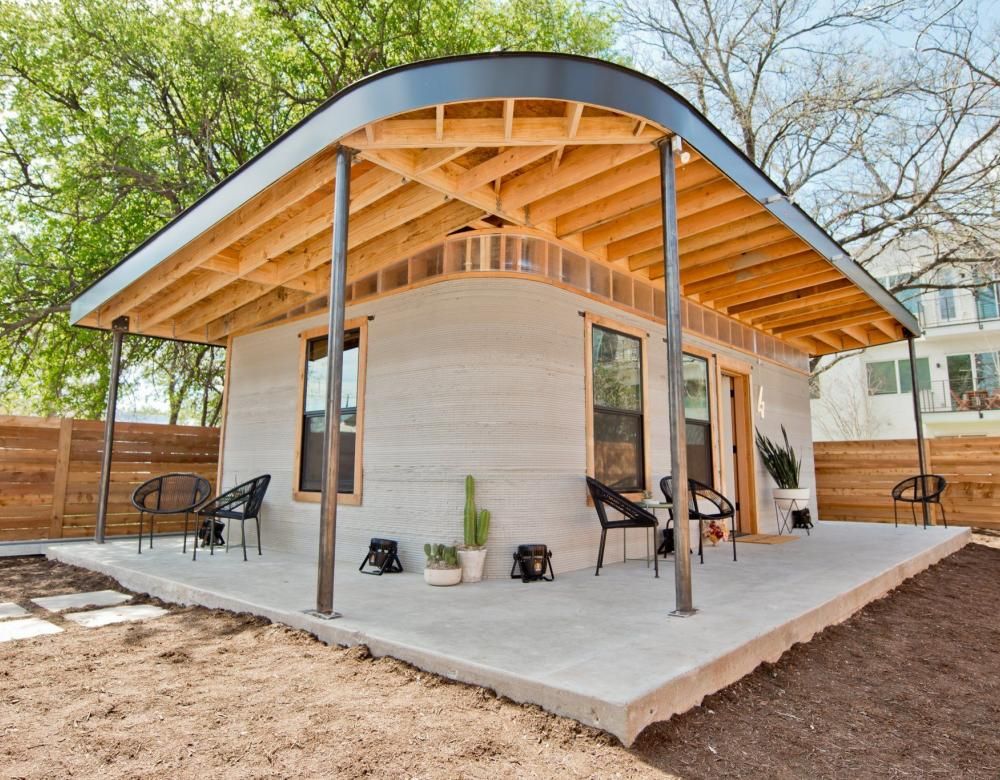
Innovation to help the world’s neediest
The 3D printing process is both high-tech and low-cost, which is why it is of great interest to use it for building low-income housing. In late 2019, the California non-profit New Story began building around fifty 45 m2 homes for people living in extreme poverty in Mexico (photo). The walls went up in less than 24 hours at a cost of 4,000 dollars (3,500 euros). According to the organization, which had already built emergency housing in Haiti, Bolivia and El Salvador using traditional techniques, 3D printing allows them to help more families, more quickly, while adapting the arrangement of the units to the needs of each household.
Many challenges remain to be resolved
Despite its advantages, improvements need to be made to 3D printing before it can rival conventional techniques.
There are still problems involved in building houses using 3D printing. Not least among them is the issue of reproducibility, since it is still difficult to ensure the regularity of the deposited concrete bead throughout the process. Another problem is the hardening speed: sometimes a layer of concrete hasn’t the time to harden sufficiently to support the weight of the next layer. This is even more the case for small construction projects, where the time between the application of two layers is reduced, as the printer goes round it more quickly. The case of multi-storey housing also raises technical challenges, since the weight of the successive layers generates strong pressure on the lower layers. Maximum strength is usually reached after about 28 days. Setting and hardening accelerators can reduce this time to a few days, but this is still not enough for rapid construction of very tall buildings. Finally, concrete is sometimes equipped with steel reinforcing bars to enhance its strength: this is known as reinforced concrete. In the case of printed concrete, research has turned to the use of metal fibres, integrated into the concrete before extrusion, to play this reinforcing role. But a structural weakness persists at the joint between printed layers, so researchers are looking for solutions to strengthen the mesh. This would make it possible to comply with the highest safety standards, such as earthquake resistance guidelines. And, as a result, to be able to print any type of building.